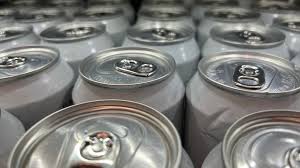
A recent report from the Aluminum Association and the Can Manufacturers Institute reveals a concerning trend: the recycling rate for aluminum beverage cans has fallen to its lowest point in over 30 years. In 1990, the rate stood at 52%, but by 2023, it had declined to just 43%.
Mark Rea II, general manager of supply and trading at Georgia-Pacific Recycling, attributes this drop to multiple causes. One key issue is the rise of single-stream recycling, where all recyclables are collected in one bin. While this method has made recycling more convenient overall, it often results in contamination—particularly with aluminum—which current processing technologies struggle to address. As a result, a portion of aluminum collected through this method is ultimately unusable.
Rea also cited a widespread lack of public understanding about which types of aluminum can be recycled and noted that recycling incentives are inconsistent and unevenly promoted. While some areas offer rewards like deposit refunds, tax breaks, and rebates for curbside recycling, these programs vary greatly across regions, and many residents are unaware they exist.
This decline in recycling has ripple effects throughout the industry. A lower supply of recycled aluminum leads to increased reliance on virgin aluminum, which is more expensive to produce due to high energy demands. This, in turn, drives up the cost of aluminum products.
Scott Biondich, president of Packaging Innovation and Design LLC, emphasized that the industry must take more responsibility in educating consumers about aluminum recycling’s benefits. He believes organizations such as the Aluminum Association and Can Manufacturers Institute should ramp up their outreach efforts.
Another major issue is the technological limitations of recycling facilities, many of which lack efficient equipment to properly separate aluminum from contaminated waste. Daniel Mendes, country business manager at Wyda Packaging, highlighted how a combination of outdated infrastructure, inconsistent recycling policies, and public disengagement have all played a role in the decline.
Mendes noted that reduced recycling rates not only pose environmental challenges but also create economic strain. With a growing demand for high-quality aluminum and limited supply, businesses face increased costs and are often forced to rely on imported or newly produced aluminum.
Blake Gordon, general manager of digital trading at Georgia-Pacific Recycling, pointed out that many small and medium-sized businesses are excluded from the recycling ecosystem. These companies often lack the volume or knowledge to participate and, as a result, send recyclable materials to landfills.
To address this, Georgia-Pacific launched hubbIT, a digital platform that provides transparent pricing and streamlines access to the recycling market for smaller waste producers.
Gordon also highlighted positive developments within the industry. For example, Waste Connections, a major recycling company, has invested heavily in upgrading facilities—such as rebuilding its Material Recovery Facility (MRF) in Plainfield, Illinois, and launching a high-tech sorting center in Colorado, scheduled to open in 2026. This new facility is expected to process up to 62,000 tons of recyclables annually using AI-driven automation.
Industry leaders are working to reverse the decline by advocating for improved policies, expanding incentive programs, and investing in advanced recycling technology. Mendes believes the path forward lies in standardizing national recycling practices, increasing public awareness, and fostering stronger partnerships between industry stakeholders and local communities.
With the global push for sustainability and aluminum’s potential for repeated recycling, experts remain hopeful. Gordon concluded by stressing that aluminum is one of the most recyclable materials available and that continuous innovation is essential for a more sustainable future.
Mark Rea II, general manager of supply and trading at Georgia-Pacific Recycling, attributes this drop to multiple causes. One key issue is the rise of single-stream recycling, where all recyclables are collected in one bin. While this method has made recycling more convenient overall, it often results in contamination—particularly with aluminum—which current processing technologies struggle to address. As a result, a portion of aluminum collected through this method is ultimately unusable.
Rea also cited a widespread lack of public understanding about which types of aluminum can be recycled and noted that recycling incentives are inconsistent and unevenly promoted. While some areas offer rewards like deposit refunds, tax breaks, and rebates for curbside recycling, these programs vary greatly across regions, and many residents are unaware they exist.
This decline in recycling has ripple effects throughout the industry. A lower supply of recycled aluminum leads to increased reliance on virgin aluminum, which is more expensive to produce due to high energy demands. This, in turn, drives up the cost of aluminum products.
Scott Biondich, president of Packaging Innovation and Design LLC, emphasized that the industry must take more responsibility in educating consumers about aluminum recycling’s benefits. He believes organizations such as the Aluminum Association and Can Manufacturers Institute should ramp up their outreach efforts.
Another major issue is the technological limitations of recycling facilities, many of which lack efficient equipment to properly separate aluminum from contaminated waste. Daniel Mendes, country business manager at Wyda Packaging, highlighted how a combination of outdated infrastructure, inconsistent recycling policies, and public disengagement have all played a role in the decline.
Mendes noted that reduced recycling rates not only pose environmental challenges but also create economic strain. With a growing demand for high-quality aluminum and limited supply, businesses face increased costs and are often forced to rely on imported or newly produced aluminum.
Blake Gordon, general manager of digital trading at Georgia-Pacific Recycling, pointed out that many small and medium-sized businesses are excluded from the recycling ecosystem. These companies often lack the volume or knowledge to participate and, as a result, send recyclable materials to landfills.
To address this, Georgia-Pacific launched hubbIT, a digital platform that provides transparent pricing and streamlines access to the recycling market for smaller waste producers.
Gordon also highlighted positive developments within the industry. For example, Waste Connections, a major recycling company, has invested heavily in upgrading facilities—such as rebuilding its Material Recovery Facility (MRF) in Plainfield, Illinois, and launching a high-tech sorting center in Colorado, scheduled to open in 2026. This new facility is expected to process up to 62,000 tons of recyclables annually using AI-driven automation.
Industry leaders are working to reverse the decline by advocating for improved policies, expanding incentive programs, and investing in advanced recycling technology. Mendes believes the path forward lies in standardizing national recycling practices, increasing public awareness, and fostering stronger partnerships between industry stakeholders and local communities.
With the global push for sustainability and aluminum’s potential for repeated recycling, experts remain hopeful. Gordon concluded by stressing that aluminum is one of the most recyclable materials available and that continuous innovation is essential for a more sustainable future.